Common problems in using effect of belt press
Time:2021-04-07 09:17 Browse:277
Common problems in the use effect of belt press: the use effect of belt press, the influence of its mechanical part is divided into adjustable factors and non adjustable factors, which are explained respectively. First of all, we understand its principle, and then we can effectively control it in use. What are the mechanical factors that cannot be adjusted?
A. Drum diameter and effective length
The bigger the diameter of the drum is, the longer the effective length is, the larger the effective settlement area is, the larger the treatment capacity is, and the longer the residence time of the material in the drum is. At the same speed, the greater the separation factor is, and the better the separation effect is. However, due to the limitation of materials, the diameter of the centrifuge drum can not be increased without limitation, because with the increase of diameter, the maximum allowable speed will decrease with the decrease of material firmness, and the centrifugal force will also decrease accordingly. Generally, the diameter of the drum is 200-1000MM and the length diameter ratio is 3-4. Nowadays, the development of centrifugal sludge dewatering machine tends to high speed and large aspect ratio, which is more suitable for the treatment of low concentration sludge and has better sludge quality. In addition, in the case of the same processing capacity, the centrifuge with large drum diameter can operate at a lower differential speed, because the screw with large drum diameter has larger slag conveying capacity. In order to achieve the same slag conveying capacity, the centrifuge with small drum diameter must improve the differential speed.
B. Half cone angle of drum
When the sediment on the inner side of the drum of the belt press is pushed to the discharge port along the cone end of the drum, it is affected by the downward sliding reflux force due to the centrifugal force. The half cone angle of the drum is an important parameter in centrifuge design. In terms of clarification effect, the cone angle should be as large as possible, while in terms of slag conveying and dehydration effect, the cone angle should be as small as possible. Because conveying slag is a necessary condition for centrifuge to work normally, the best design must first satisfy the condition of conveying slag. For difficult separation materials such as activated sludge, the half cone angle is generally within 6 degrees, so as to reduce the reflux speed of sediment. For ordinary materials, the smooth transportation of sediment can be ensured when the half cone angle is less than 10 degrees.
C. Pitch
Pitch, that is, the distance between two adjacent spiral blades, is a very important structural parameter, which directly affects the success or failure of slag transportation. When the screw diameter is fixed, the larger the pitch is, the larger the spiral angle is, and the greater the chance of material blocking between the screw blades is. At the same time, large pitch will reduce the number of turns of the spiral blade, resulting in uneven distribution of materials at the cone end of the drum and increase the vibration of the machine. Therefore, for difficult separation materials such as activated sludge, it is difficult to transport slag. The screw pitch should be smaller, generally 1 / 5 ~ 1 / 6 of the drum diameter, so as to facilitate transport. For easily separated materials, the pitch should be larger, generally 1 / 2 ~ 1 / 5 of the drum diameter, so as to improve the conveying capacity of sediment.
D. Spiral type
Screw is the main component of centrifugal sludge dehydrator. Its function is to transport the sediment settled inside the drum and smoothly discharge the sediment. It is not only a discharging device, but also determines the production capacity, service life and separation effect.
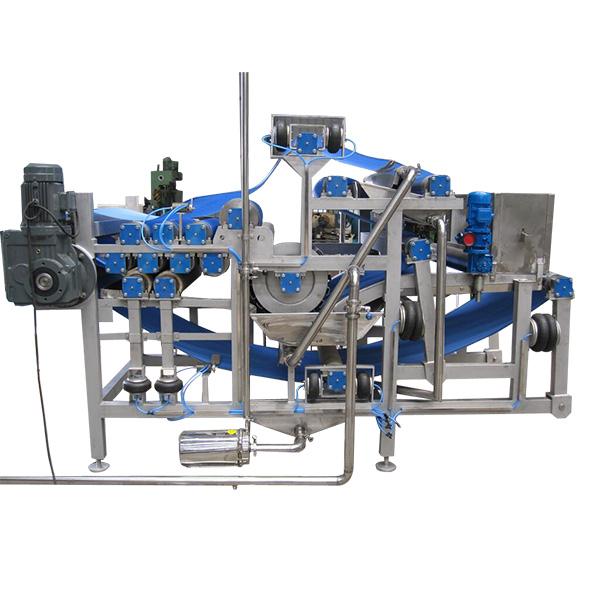
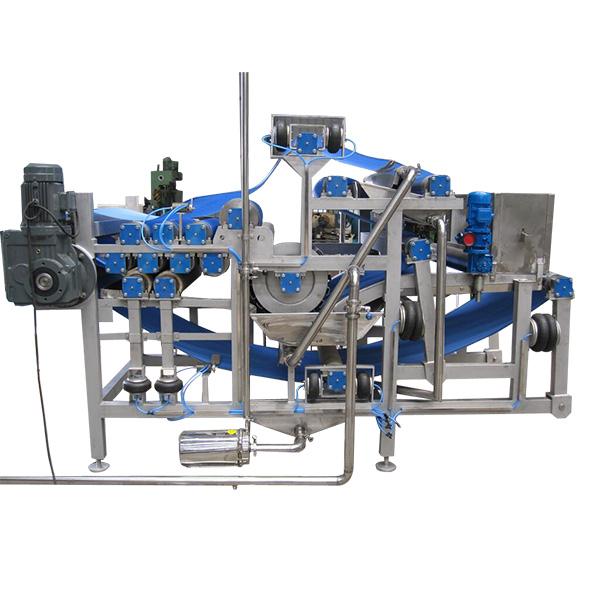