Introduction of automatic tomato sauce production line
Time:2021-04-07 15:28 Browse:277
1. Introduction of ketchup production line
Including the original fruit lifting system, cleaning system, sorting system, crushing system, preheating and enzyme killing system, beating system, vacuum concentration system, sterilization system, sterile bag filling system.
The production capacity includes: 150 tons of raw materials (fresh tomatoes, peppers, apples, strawberries, blackberries, carrots, onions, etc.), 300 tons, 400 tons, 500 tons, 600 tons, 800 tons, 1000 tons, 1200 tons, 1500 tons.
The final product concentration is: 28-30brix, 30-32 brix, 36-38 Brix (can be adjusted according to the customer's product index)
Less than 300 tons can be controlled manually or automatically.
The whole line can process strawberry jam, blackberry jam, blueberry jam, raspberry jam, apple jam, mango jam, apricot jam, carrot jam, onion jam, chili jam and other concentrated fruit and vegetable products.
2、 Function characteristics of tomato sauce production line
(1) Equipped with multi-function crusher, it can produce onion paste, carrot pulp, chili sauce, apple pulp, strawberry pulp, blackberry pulp and other jam products.
(2) With the special effect of crusher and low temperature concentration (1) the effective evaporation temperature is less than 70 ℃, the residence time of materials in evaporator is shorter, and the loss of red pigment (tomato sauce) and other nutrients is less than that of similar equipment at home and abroad.
(3) The power consumption of the same output device at home and abroad is less than that of the same output device at home and abroad.
(4) The evaporator is equipped with condensate secondary steam recovery system, which can significantly reduce steam consumption.
(5) The structure of the material mixing device in the sterilizer is different. Compared with other similar equipment, the structure is simple and does not scale. At present, there is scaling phenomenon in the material pipeline of any similar equipment at home and abroad, which affects the heat transfer effect and product quality.
6. In the filling process, the rotary table lifting mode is adopted to avoid the secondary pollution.
The double channel refiner adopts the conical screen structure, the gap with load can be adjusted, and the frequency control of twice beating makes the semi-finished products more delicate
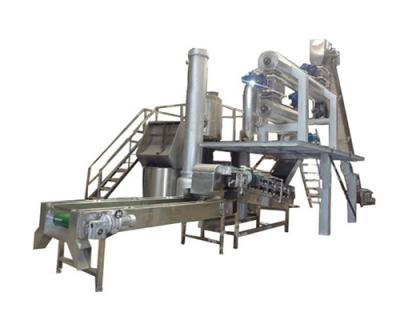
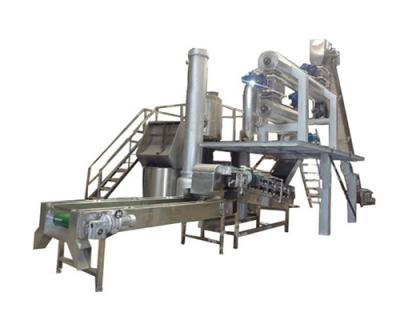